Presently, the global landscape grapples with the intricacies of resource utilization and the escalating specter of resource depletion. Amidst the accelerating depletion of resources, the imperative to bolster resource efficiency has ascended as a linchpin in propelling production development. As societal and economic progress hurtles forward, the burgeoning requisites for enhanced quality of life and elevated living standards have underscored the exigency for more astute resource utilization. In this context, the circulating fluidized bed boiler(CFB Boilers), an innovative energy-conservation technology within industrial production, assumes a pivotal role in safeguarding ecological integrity through its heightened efficiency and recycling competencies. Conspicuously, it holds the promise of significantly amplifying the reutilization of particulate residues.
The global industrial landscape increasingly embraces the circulating fluidized bed boiler (CFB Boilers), deftly addressing the prevailing demands of industrial growth. Recent years have witnessed rapid strides in circulating fluidized bed boiler (CFB Boilers) technology, positioning it as an eminent energy-efficient solution. It methodically dissects energy losses, facilitating the realization of prudent energy-saving practices and consumption reductions. Of particular significance is the current state of global resource utilization, characterized by pronounced energy losses due to the pervasive scarcity of resources. Thus, this study embarks on an optimization endeavor, centered around the analysis of the circulating fluidized bed boiler (CFB Boilers) system. Notably, it homes in on the boiler furnace air system, dust collector operations, sewage heat loss control, and the energy-saving system network. This comprehensive inquiry aims to augment the energy efficiency of the circulating fluidized bed boiler, steadfastly committed to energy-saving imperatives. By continually refining the operational processes of the circulating fluidized bed boiler, the study seeks to mitigate the squandering of pivotal resources and promote a more judicious approach to resource management.
1 Overview of Circulating Fluidized Bed Boilers (CFB Boilers)
1.1 Introduction to Circulating Fluidized Bed Boiler (CFB Boilers)
The circulating fluidized bed boiler (CFB Boilers), depicted in Figure 1, stands as a burgeoning energy-conservation technology with global significance. It finds primary application within the realm of clean coal combustion and industrialized technologies, serving as a pivotal asset in China’s energy landscape. At its core, fluidized combustion reigns as the prevailing combustion methodology within circulating fluidized bed boilers (CFB Boilers), adeptly executed within both the combustion chamber and the cyclic return furnace.
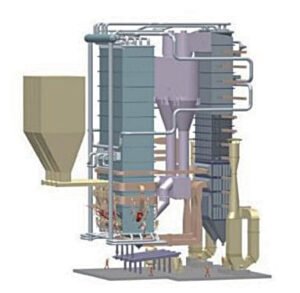
While sharing similarities with other combustion methods like bubbling fluidized beds, circulating fluidized bed boiler (CFB Boilers)technology possesses distinct operational differentiations. Notably, it operates at an elevated wind speed, a factor pivotal in significantly augmenting combustion and desulfurization efficacy. This enhanced operational feature, coupled with the potential for expanded boiler capacity, underscores the compelling advantages of circulating fluidized bed boilers (CFB Boilers).
Throughout its practical application, circulating fluidized bed boiler (CFB Boilers) technology has impressively surmounted a myriad of challenges rooted in thermodynamics, mechanics, and materials science. However, in the realm of energy-saving efficiency, there remains room for further optimization. Particularly, the optimization efforts should be directed towards refining energy efficiency in the primary combustion processes within the combustion chamber and the subsequent cyclic return to the furnace. This targeted enhancement endeavors to propel the technology’s energy efficiency to greater heights.
1.2 Characteristics of Circulating Fluidized Bed Boilers (CFB Boilers)
Within the context of China’s prevailing energy landscape, the application of circulating fluidized bed boilers (CFB Boilers) in coal power stations stands as a robust and progressively expanding phenomenon. This emerging development presents a paradigm shift characterized by heightened efficiency and reduced pollution, constituting a novel and advanced furnace model. Notably, circulating fluidized bed boilers (CFB Boilers) are endowed with distinctive optimization attributes. Their versatility in fuel adaptation is notably expansive, facilitating effective combustion of high-quality coal and even accommodating the incineration of lower-grade fuels. This attribute is particularly significant given the presence of underutilized resource reserves and the domestic utilization of specialized bed boilers precipitates furnace desulfurization, culminating in a significant reduction in sulfur dioxide emissions. Simultaneously, the integration of ancillary technologies, such as denitrification processes, works in tandem to sustain requisite temperatures within the cyclone separator region. This multifaceted approach guarantees the mitigation of pollutants.
Circulating fluidized bed boilers (CFB Boilers) additionally exhibit formidable load regulation capabilities, aligning with elevated unit energy consumption levels. These attributes are paralleled by rigorous automation and control requisites, solidifying their status as a ubiquitous and pioneering energy-saving technology extensively adopted within China’s industrial landscape.
1.3 Applications of Circulating Fluidized Bed Boilers (CFB Boilers)
The contemporary utilization of circulating fluidized bed boilers (CFB Boilers) bears substantial practical significance, underscored by robust commercial viability and technological prowess. These boilers manifest commendable coal adaptability and combustion efficiency, endowing them with a competitive edge. Recent years have witnessed the deployment of circulating fluidized bed boilers (CFB Boilers) in diverse sectors of clean coal power generation across China. In this realm, these boilers exhibit commendable combustion stability and fuel adaptability, although challenges persist in realizing economically viable applications across a spectrum of coal materials with disparate characteristics.
Significantly, the evolving landscape of China’s coal power supply has necessitated the usage of an array of coal materials, particularly amid resource constraints. This imperative has led to the widespread utilization of lower-quality coal, thereby engendering notable declines in the thermal efficiency of coal power plants and concomitantly augmenting coal consumption. Although the current technological application of circulating fluidized bed boilers (CFB Boilers) in China showcases several merits, certain technological limitations prevail. When comprehensively examined, these limitations manifest in elevated unit maintenance demands attributable to substantial variations in coal quality. This, in turn, contributes to escalated coal consumption and diminished operational economic viability, thereby prompting the need for comprehensive enhancements in energy-saving efficiency within the realm of circulating fluidized bed boiler technology.
Consequently, addressing these challenges and ameliorating the energy-saving efficacy of circulating fluidized bed boiler technology emerges as a salient and imperative pursuit.
2 Working Principle and Structure of Circulating Fluidized Bed Boiler (CFB Boilers)
The operational dynamics of a circulating fluidized bed boiler are predicated on the velocity of its gas flow, which in turn gives rise to a spectrum of distinct particle states—namely, fixed bed, bubbling fluidized bed, turbulent fluidized bed, and fast fluidized bed. The circulating fluidized bed, primarily situated within the ascending phase, predominantly operates under the influence of rapid fluidization and hydrodynamic properties, thereby defining its journey. In tandem, solid materials undergo fluidization propelled by gas flow velocities surpassing that of individual particles. Consequently, these particles exhibit vertical motion akin to a particle mass, engendering pronounced remixing, multi-directional particle movement, and the continual formation and dissolution of particle aggregates. This dynamic fluid state permits the gas flow to transport sizable particles, ensuring their terminal velocity greatly exceeds the velocity of the adjacent gas cross-section.
The architecture of a circulating fluidized bed boiler comprises integral components such as a cyclone separator, furnace, dust collector, slag chiller, and air preheater. Typically adopting a single drum design, it is subdivided into chambers such as the air chamber, dense phase zone, and dilute phase zone, facilitated by natural circulation. This encompassing configuration extends to include auxiliary features like the coal economizer, reclaimer, and air preheater. At the core of this setup, the cyclone separator assumes a pivotal role. This central structure interfaces with the combustion chamber, fulfilling both the role of internal partition and facilitating separation. Additionally, it interfaces with the ash cooler, thereby ensuring the seamless and normal operation of the circulating fluidized bed boiler in its entirety.

3 Energy-Saving Technology Analysis of Circulating Fluidized Bed Boiler
3.1 Energy-Saving Technology through Low Bed Pressure Operation
In the current landscape of China’s circulating fluidized bed boiler manufacturing, the focus is primarily on striking a balance between cost control and adherence to pollution emission standards, thereby fostering notable advantages. Within this context, circulating fluidized bed boiler manufacturing in China has evolved into a pivotal facet of industrial production and resource utilization, propelled by energy-saving technologies. One prominent approach involves fluid restructuring to enhance the quality of essential bed material, concurrently leading to a reduction in material demand. This strategic reduction facilitates the effective lowering of bed pressure during operation, consequently achieving a reduction in fan energy consumption.
Illustratively, the widely used supercritical air-cooled circulating fluidized bed boiler in China exemplifies the successful integration of low bed pressure operation at a technical level, yielding conspicuous energy-saving outcomes. The efficacy of energy-saving measures within circulating fluidized bed boilers (CFB Boilers) hinges upon the precise configuration of the system according to fluid flow patterns and stringent fuel requirements within the screening system. The application of low bed pressure operation technology strives to bolster energy-saving efficiency through continuous optimization of the cyclone separator in the circulating fluidized bed boiler. This, in turn, ensures the maintenance of optimal bed pressure and the exclusion of larger slag particles from circulating within the boiler. Consequently, the back pressure of the water-cooled air chamber in the circulating fluidized bed boiler is effectively reduced, thereby contributing to enhanced energy-saving prospects.
3.2 Strategic Start-Up Time Arrangement
To diligently enhance the prevailing energy-saving impact of circulating fluidized bed boilers (CFB Boilers), a more stringent set of prerequisites and protocols should be established within the circulating fluidized bed boiler system. One such imperative pertains to meticulous preparatory measures and meticulous inspection of oil guns in advance. This measure squarely aims at diminishing the frequency of oil gun interventions during the ignition phase of the circulating fluidized bed boiler. Simultaneously, a methodical approach should be adopted for orchestrating the commencement of the external bed operations. In cases where bed temperature attains elevated levels, swift mobilization of the external bed should be executed, accompanied by a measured increase in coal input to optimize the operation. This, in turn, facilitates the judicious manipulation of the ash control valve aperture, culminating in the stabilization of bed temperature dynamics.
Within the realm of circulating fluidized bed boilers (CFB Boilers), the role of the steam engine is of paramount significance. Its synchronization with the commencement timeline is pivotal and demands a judicious and scientifically grounded arrangement. Subsequent to the initiation of boiler operations, the steam engine should be attuned to the prevailing environmental conditions, thereby enabling a seamless cycle of operation. This deliberate synchronization ensures the unfaltering execution of combustion and circulating fluidization processes, thereby upholding operational normalcy.

3.3 Dust Collector Energy-Saving Technology
The circulating fluidized bed boiler stands as a cornerstone within the contemporary energy-saving technology landscape. To effectively enhance the energy-saving efficiency of circulating fluidized bed boilers (CFB Boilers), paramount attention must be paid to ensuring both combustion efficacy and ash content alignment with national emission standards for thermal power plants. This endeavor necessitates a harmonious synergy between local governmental policies, pollutant emission criteria, and the operational parameters of circulating fluidized bed boilers (CFB Boilers). A pivotal facet of this synergy revolves around the construction and operational efficiency of dust collectors.
Within the framework of advancing the comprehensive energy-saving technology of circulating fluidized bed boilers (CFB Boilers), meticulous optimization and enhancement of dust collector ash removal mechanisms become imperative. While the bag filter within the circulating fluidized bed boiler engenders a measure of ash removal efficacy, it is essential to acknowledge its limitations in attaining ultra-low emission targets. This limitation is especially pronounced in instances of heightened resistance, accentuating energy consumption inefficiencies. Accordingly, the meticulous construction of the dust collector warrants stringent optimization.
A judicious approach involves aligning dust collector design with the ash content of the coal in consideration. By holistically integrating this factor, effective dust collector control can be realized, thereby facilitating the utilization of coal blending to engender the optimal operational state of the circulating fluidized bed boiler. This meticulous orchestration underpins the normal operation of the fluidized bed boiler, ensuring the harmonization of combustion efficiency and emission standards.
3.4 Optimal Bed Material Thickness and Particle Size for Effective Start-Up
Adhering to the prescribed setup requisites of circulating fluidized bed boilers (CFB Boilers) in China, the enhancement of energy-saving efficiency hinges on two crucial facets: ensuring the normal combustion volume within the boiler and facilitating its seamless warm-up process. Concomitant with the boiler’s regular start-up, judicious utilization of precise control mechanisms during the start-up phase assumes paramount importance, specifically pertaining to the manipulation of bed material thickness and particle size.
In the realm of energy-saving operation for circulating fluidized bed boilers (CFB Boilers), a nuanced approach underscores the intrinsic characteristics of the circulating material. It entails leveraging the stabilization potential of larger particles to regulate bed temperature, concomitant with the strategic deployment of boilers to heat finer particles. This stratagem ensures the incorporation of a certain level of bed material coarseness into the boiler process, optimizing overall efficiency.
In cases where the circulating fluidized bed boiler experiences short-term shutdowns, swift re-ignition mandates the consideration of bed pressure. To mitigate elevated pressures, the strategic placement of the ash pipe utilizing the reclaimer and cold slag device effectively curtails the accumulation of material within the boiler. This tactical measure accelerates the heating process of the bed, resulting in an augmented temperature curve and consequently abbreviated start-up durations for circulating fluidized bed boiler units. This strategic orchestration plays a pivotal role in streamlining operational efficiency and promoting energy-saving objectives.
3.5 Fan Energy-Saving Technology through Frequency Conversion Speed Control
Upon a comprehensive assessment of China’s circulating fluidized bed boiler engineering practices, a discernible pattern emerges: the prevalent employment of centrifugal fans due to their capacity to generate high wind pressures. While this choice yields commendable efficiency, it concurrently contributes to elevated energy consumption levels. To effectively address this energy-saving imperative, a structural transformation in the centrifugal fan system can be orchestrated, marked by the adoption of frequency converters in conjunction with centrifugal fans. This innovative approach not only bolsters economic viability but also serves as a catalyst for energy conservation.
An exemplary manifestation of this strategy pertains to the primary fan speed control within the widely utilized circulating fluidized bed boiler. By integrating a frequency conversion device, the axial power of the centrifugal fan is notably diminished, concurrently reducing the associated power consumption rate. A concrete illustration of this transformative measure indicates that within a circulating fluidized bed boiler employing the primary fan speed control and equipped with a frequency conversion device, substantial energy savings of up to 9,370,000 kWh can be realized. This outcome underscores the potent energy-saving benefits inherent to this approach, a sentiment further corroborated by the concomitant energy-saving impact witnessed within the secondary fan.
This strategic embrace of frequency conversion speed control for fans, especially within the context of the primary fan system, accentuates a judicious balance between operational efficiency and energy conservation, distinctly contributing to the overarching energy-saving goals of circulating fluidized bed boilers (CFB Boilers).
In conclusion, the circulating fluidized bed boiler stands as an indispensable and innovative energy-saving technology that plays a pivotal role in China’s production and developmental landscape. Its practical utility and scientific advancements contribute significantly to the country’s progress. Particularly in the context of resource management and utilization, the circulating fluidized bed boiler assumes a multifaceted role. Its optimization necessitates a holistic approach, encompassing environmental considerations, structural enhancements, and tailored strategies aligned with its operational characteristics.
The imperative for effective energy conservation within the framework of the circulating fluidized bed boiler underscores the need for targeted measures. These measures should address both the operational intricacies of the boiler system and the broader context of resource utilization, aiming to curtail avoidable energy losses. By conducting a comprehensive analysis and optimization of the energy-saving technology encompassing the circulating fluidized bed boiler, the efficiency of industrial development at large can be tangibly augmented. Such advancements, in turn, pave the way for the eco-friendly and efficient utilization of low calorific value coal, thus substantiating a greener and more sustainable trajectory for China’s energy landscape.
[Source] Lu Yongsheng, Research on energy saving technology of circulating fluidized bed boiler, Energy Conservation and Emission Reduction 2023[2]:242-244
DHB Boiler
Discover The Superior Quality And Cutting-Edge Technology Of DHB Boilers. Explore Our Range Of Biomass Boilers, Waste Heat Boilers, And More. Take Your Industrial Operations To New Heights With DHB Boiler.