To achieve a low-carbon, environmentally sustainable society, the adoption of renewable fuels like biomass and waste presents promising alternatives to coal and oil for power generation. However, the corrosive nature of the heating surface environment in plant boilers utilizing these fuels surpasses that of fossil fuels. Particularly in biomass and waste incinerators, the water-cooled walls and superheaters experience significantly shortened service life, often resulting in costly unplanned downtime.
In recent years, there has been a gradual shift in steam temperatures within waste incineration boilers, progressing from 400 °C to 500 °C, and even reaching 540 °C in some biomass power plants. During the combustion processes involving biomass or waste, boiler steam temperatures are typically maintained below 450 °C to prevent high-temperature corrosion. Further elevating steam temperatures can lead to noteworthy increases in corrosion rates in biomass or waste-to-energy plants. Several factors contribute to this issue, including (1) the utilization of fuels containing alkali metals, heavy metals, Cl, and S; (2) fluctuations in flue gases; (3) high-velocity, fly ash-coated flue gases; and (4) deposition of pollutants on the heating surface. These challenges exacerbate the durability and efficiency of the systems.
To combat the challenges posed by corrosive conditions, power plant boiler heating surfaces demand robust, highly ductile, and producible alloys. Researchers have invested considerable effort in developing such alloys; however, the pursuit of these goals doesn’t always directly lead to high oxidation and corrosion resistance. For instance, in certain alloys, the addition of Al/Cr enhances oxidation and high-temperature corrosion resistance. However, beyond a specific threshold, these elements may reduce the creep strength of the alloy. Achieving both high strength and high corrosion resistance necessitates the separation of these functions. As a result, coating/substrate systems emerge as a viable technical solution.
In this approach, the base alloy provides the load-bearing capacity, while the coating’s role is to furnish a metallic surface composition that interacts with the environment to generate a protective oxide film. This protective film serves to safeguard the substrate from corrosive substances effectively. To achieve this, the coating should possess a high-density, low porosity microstructure, along with resistance to cracking and spalling due to thermal shock and flue gas corrosivity. Moreover, effective coatings must restrict the diffusion of substrate elements into the surface coating. By carefully balancing these factors, coating/substrate systems offer a promising strategy to address the corrosive challenges in power plant boilers.
The pursuit of high thermal efficiency and cost-effectiveness in biomass or waste incineration plants has highlighted the significance of developing low-cost and highly durable materials, as well as efficient application processes. To achieve this, advanced refractory materials have been employed to ensure optimal hearth performance, preventing high-temperature damage and ash plugging. In water-cooled walls, anti-corrosion coatings such as tiles, metal-sprayed layers, and nickel-based alloy overlays have gained widespread usage.
Superheater protection has also seen advancements with the adoption of tubes exhibiting excellent corrosion resistance. To further enhance protection against corrosion in critical areas, suitable protective coatings like metal-ceramic coatings, ceramic coatings, and laser cladding coatings have been developed. Additionally, to improve the durability of high-temperature and high-pressure boiler materials, optimizing boiler design has become essential in mitigating high-temperature corrosion and scouring of superheater and water-cooled wall tubes.
This paper serves as a comprehensive review encompassing the operational modes, severe corrosion conditions, and corrosion mechanisms observed in waste power station boilers. It delves into the research progress made in anti-corrosion materials and coatings for incinerator hearths, water-cooled walls, and superheater heated surfaces. Furthermore, it provides an outlook on future research directions in this crucial domain.
Refuse incinerator
1.1 Corrosive environment of waste incinerator boiler heating surfaces
Boilers designed to burn various types of biomass or refuse fuels, including domestic waste and residues like straw, peat, wood chips, bark, and rice husks, are subject to a highly corrosive environment. In comparison to boilers burning fossil fuels, these systems experience greater fluctuations in gas temperatures and compositions. The combustion gases generated during the process yield substantial quantities of low melting point deposits enriched with high concentrations of chlorides. Notably, the presence of corrosive gases such as Cl2, HCl, alkaline chlorides, and moisture accelerates the corrosion rate of power plant components, particularly impacting water-cooled walls and superheater tubes of the boiler heating surfaces.
During operation, alkaline chloride deposits form on boiler components, causing a dual effect: diminishing heat transfer and triggering corrosion. This combination leads to significant material wastage, tube failures, tube leakage, unplanned downtime, and shortened component life. Consequently, it severely impairs the thermal and electrical efficiency of the power plant, incurring substantial maintenance, replacement, and outage costs. Some Waste-to-Energy (WTE) power plant boilers attempt to address corrosion issues by reducing steam temperatures; however, this approach notably limits the electrical efficiency of the power plant.
1.2 Corrosion mechanism of waste incinerator boiler heating surfaces
The corrosion observed in waste incinerators predominantly stems from chloride-induced corrosion, with the following key mechanisms at play:
- Chloride-induced reactive oxidative corrosion.
- Electrochemical corrosion.
- Corrosion based on molten salts.
While sulfur-containing compounds may influence alloy properties to some extent, the primary mechanism contributing to material failure is associated with chlorine-containing compounds existing in gaseous, liquid, or solid states. These corrosive agents play a pivotal role in the degradation of the boiler heating surfaces within waste incinerators.
1.2.1 Reactive Oxidation Mechanisms of waste incinerator boiler heating surfaces
Zahs et al. conducted a thorough investigation into the reactions of chlorine-containing compounds with alloying elements present in boiler components. The relevant reaction equations (Eqs. 1 to 3) shed light on the mechanisms involved. One commonly assumed process is the generation of Cl2 through the Deacon reaction (Eq. 1), which typically occurs at a slow rate but can be catalyzed by oxidized metal surfaces. Cl2 can also form when chlorine-containing salts (e.g., KCl) within deposits react with previously formed oxidized films (e.g., Cr2O3) in the presence of O2 (Eq. 2). Furthermore, this reaction can take place in the presence of both O2 and H2O, as shown in equation (3). The produced Cl2 migrates to the surface of the alloy via defects, such as pores or cracks in the oxide layer, and subsequently reacts with it to create chlorides.
The formation of metal chlorides is expedited in oxygen-deficient environments. When temperatures exceed 400 °C, metal chlorides evaporate and diffuse outward into the gas phase. Once an ample oxygen supply is available, gaseous metal chlorides convert back into oxides. The newly generated oxide forms within cracks and pores of the existing oxide film, leading to subsequent rupture and flaking of the oxide film. Notably, metal chlorides (occurring at low oxygen partial pressure) are often observed at the metal/sediment interface, whereas the deposit’s exterior predominantly contains metal oxides (occurring at high oxygen partial pressure). In this process, Cl2 molecules must diffuse through the oxide layer, presumably through sizeable defects like cracks and pores. At elevated temperatures, the vapor pressure of metal chlorides may be substantial, causing volatile chlorides to diffuse towards the oxygen-rich outermost layer of the scale (high oxygen partial pressure). Here, they react with oxygen, resulting in the formation of metal oxides.
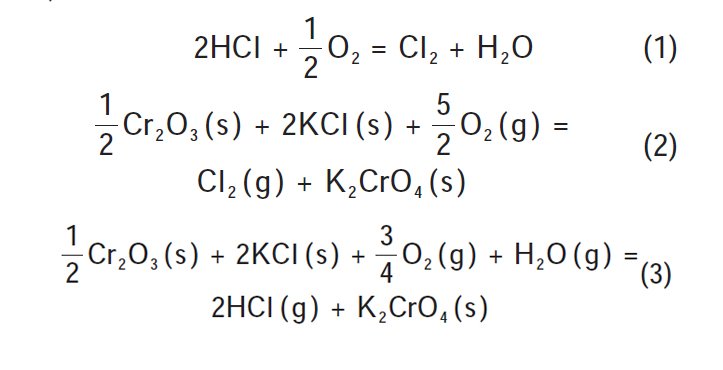
1.2.2 Electrochemical corrosion mechanism of waste incinerator boiler heating surfaces
Jonsso et al. conducted a comprehensive investigation from an electrochemical perspective, revealing the corrosion mechanism of alkali metal chlorides. Their study involved environmental scanning electron microscope (ESEM) observations to explore the impact of KCl on the initial oxidation stage of T22 steel at 400 and 500 °C. Based on the study’s findings, a novel corrosion mechanism was proposed, highlighting the significance of Cl- in alkali metal chlorides as a key factor in accelerating corrosion. It was observed that Cl intrudes into the metal surface in the form of Cl-.
The reaction equations of the Cl- diffusion mechanism are represented by Eqs. (4) to (7). At the metal/oxidation interface, Fe in the metal matrix exists in the form of Fe2+ due to the metal’s exposure to oxygen (Eq. (4), (5), and (6), and (7)). Initially, alkali metal chlorides undergo a transformation from a solid to a molten state at the surface of the alloy oxide layer. In the presence of molten KCl and water vapor, oxygen reduction occurs at the oxide surface, leading to the formation of KOH, which releases Cl- (Eq. (6)).
Due to Cl-‘s low charge/radius ratio compared to O2, it rapidly moves along the oxide grain boundaries to reach the interface between the metal and the oxide layer, where it reacts with Fe2+ to form FeCl2 (Eq. (7)). FeCl2 then swiftly volatilizes from the metal/oxide layer interface, driven by the high vapor pressure environment. This process consumes the metal and simultaneously accelerates the oxidation of the metal surface, leading to the exfoliation of the oxide layer. The presence of FeCl2 plays a crucial role in intensifying both the corrosion of the metal surface and the subsequent detachment of the oxide layer.

1.2.3 Molten Salt Corrosion Mechanisms affecting waste incinerator boiler heating surfaces
Molten alkaline chlorides display the ability to dissolve oxides of Fe, Ni, and Cr, with their solubility being influenced by alkalinity and the presence of water vapor. Field and laboratory experiments have identified molten ZnCl2 and PbCl2 as significant contributors to corrosion in the temperature range of 300 to 400 °C, primarily due to their low melting points and the formation of low melting point eutectic mixtures with other salts. During combustion processes, Pb and Zn can react with S and Cl to generate sulfates and chlorides in the flue gas. These low melting point solid or gaseous compounds may exist in the flue gas and, upon condensation, can form corrosive products on the cooler surfaces of superheater or water-cooled wall tubes as they traverse through the convection components of the boiler.
These corrosive products pose a dual threat: they not only erode the oxide film formed on the surface of the substrate, thereby accelerating substrate corrosion, but also diminish the thermal conductivity of the boiler tubes. Consequently, this limitation influences the attainable steam temperature in Waste-to-Energy boilers, ultimately reducing the electrical efficiency of the Waste-to-Energy plant. As the boiler temperature drops further, corrosive substances are more likely to condense onto the lower-temperature tube surfaces. The principal corrosion process involving metal chlorides can be represented by the following reaction equation: [Reaction equation to be inserted here.
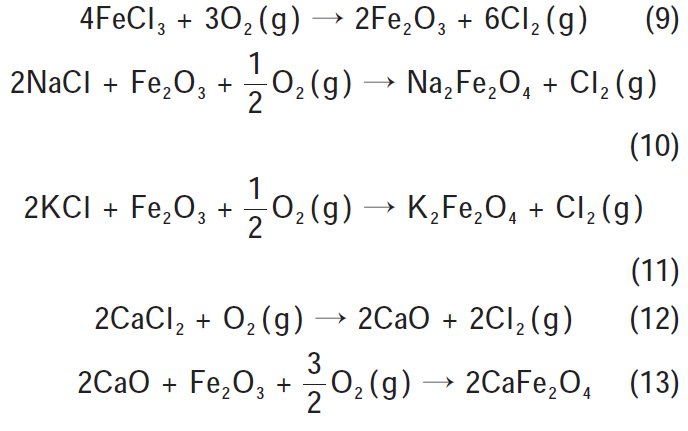
As evident from Equations 8 to 13, the corrosion of metal chlorides on the substrate primarily manifests in the detrimental impact on the oxide film. The produced Cl2 actively takes part in the corrosion process, exacerbating the degradation of the boiler heating surfaces.
Waste incinerator protection technology
To combat the corrosion challenges faced by the heating surfaces of biomass or garbage incinerators in the harsh environment mentioned above, significant strides have been made in the development and application of advanced anti-corrosive coatings and corrosion-resistant materials. Additionally, there has been considerable progress in the development of evaluation methods to assess corrosion resistance.
2.1 Furnace and water-cooled wall protection for waste incinerator boiler heating surfaces
In conventional treatment scale incinerators, most mechanical grate incinerator furnace chambers utilize air-cooled furnace wall structures. This design aims to dissipate some of the heat through air forced convection to cool the furnace wall and prevent coking on the inner side of the furnace chamber during the incineration of domestic waste with lower calorific value. However, for large incinerators, especially those burning high calorific value domestic waste, the heat load on the furnace is substantial, and the use of air-cooled furnace walls may not effectively inhibit furnace coking.
To address this challenge, water-cooled furnace walls offer a more effective solution. Water, with its higher specific heat compared to air, facilitates better heat transfer. By using water-cooled walls instead of air-cooled walls, furnace coking can be better inhibited. During operation, water from the steam bag enters the lower collector box through the descending pipe and is evenly distributed into the water-cooled wall pipes. Here, it exchanges heat with the cast refractory material and refractory bricks, effectively reducing the surface temperature of the refractory bricks to around 700-800 °C, which significantly curbs the generation, adhesion, and growth of furnace chamber coking.
Water-cooled wall tubes are typically made from carbon and CrMo steels to prevent localized corrosion inside the tubes. The metal temperature of the water-cooled wall ranges from 250 to 320 °C, while the metal temperature of the superheater surface is approximately 300 to 500 °C. As the temperature, pressure, and power generation efficiency increase, the corrosive environment becomes more severe. Therefore, addressing this challenge necessitates the development and application of corrosion-resistant materials and coatings.
Various corrosion-resistant coatings are commonly used to protect carbon steel and CrMo steel pipes, such as tiles, thermal spray coatings, cladding layers, or fusion cladding layers. These coatings play a crucial role in safeguarding the integrity and longevity of the water-cooled walls and other critical boiler heating surfaces, enabling efficient and reliable waste incineration processes.
2.1.1 Refractory materials for waste incinerator boiler heating surfaces
In a mechanical grate waste incinerator, the furnace is divided into the drying zone, combustion zone, and burnout zone. Various areas of the furnace lining, such as the waste pusher inlet area, grate side walls, front arch, rear arch, furnace roof, and slag discharge, experience different temperatures, mechanical strength, and atmospheres. Accordingly, suitable refractory materials must be selected based on the specific working conditions of each area.
Incinerator refractory materials can be broadly categorized into shaped refractory products and unshaped refractory materials. Shaped refractory products encompass clay bricks, high alumina bricks, and silicon carbide bricks. On the other hand, unshaped refractory materials include clay and silicon carbide castables, as well as high alumina plastics. In recent research, silicon carbide castables with phosphates have shown excellent wear resistance, leading to an increasing preference for their use in waste incineration projects.
Unshaped refractory materials offer exceptional construction performance, allowing for the selection of more suitable varieties based on specific incinerator conditions. However, during operation, fly ash erosion can impact oxide refractory linings. Excessive fly ash adhering to the inner wall of the furnace chamber increases the lining load, potentially causing deformation of the steel structure and lining collapse under high loads. This phenomenon occurs because silicon carbide is prone to oxidation by O2 and H2O at temperatures of 900 °C and above. The oxidation transforms silicon carbide particles into larger SiO2 particles, which subsequently expand and fracture. This issue often necessitates incinerator shutdowns for ash removal, severely affecting equipment operating efficiency.
In recent years, longer-lasting tiles have been developed and implemented as an alternative to conventional castables and plastic refractories. Typically made from high SiC or high Al2O3 materials, these tiles are applied to the outer surface of the water-cooled wall using refractory mortar. Special hooks or fixing nuts are used to secure the tiles to the refractory mortar surface. Cooled by the water-cooled wall, the surface temperature of the tile lining remains around 900 °C. Silicon carbide tiles offer chemical stability and effectively prevent damage caused by thermal stress during use, enhancing the overall durability of waste incinerator boiler heating surfaces.
2.1.2 Thermal Spray Coating for waste incinerator boiler heating surfaces
Thermal Spray Coating, which includes flame spraying, arc spraying, explosion spraying, and plasma spraying, is a widely used method to protect waste incinerator boiler heating surfaces. These technologies can produce coatings with thicknesses ranging from 150 to 800 μm. The process involves melting a large number of metal spray particles using a high-temperature heat source and then rapidly impacting and solidifying them on the substrate layer by layer.
The application of Al/80%Ni-20%Cr flame spraying layer on water-cooled walls was carried out earlier, where researchers Kawahara and Kira conducted laboratory corrosion tests to screen an Al/80%Ni-20%Cr double layer gas spraying layer. This coating was successfully applied to the water-cooled wall tube of a demonstration project in Japan, operating at a steam temperature/pressure of 280 ℃/18.5 kgf-cm-2-g-1. The coating demonstrated good durability over three years and was subsequently implemented in seven waste incineration plants in the country. However, researchers identified the main deterioration factor as the penetration of corrosive gases into the coating through defects, leading to the formation of corrosive layers and a reduction in the bonding strength between the coating and the substrate.
Yamada et al. also tested several different coatings on water-cooled wall tubes (SUS310S) using explosion spraying, supersonic flame spraying, and plasma spraying methods. After operating the samples in an actual waste incinerator for seven years, the sprayed layers remained in good condition without significant pitting or flaking. Among the coatings, the 50%Ni-50%Cr alloy sprayed layer prepared by the explosion spraying method exhibited the most outstanding performance, demonstrating good corrosion resistance with a wall thickness loss of about 1/37 of carbon steel.

From the perspective of service life, spraying efficiency, and preparation site, metal sprayed coatings are convenient to use but may suffer from lower durability compared to fully dense coatings due to the presence of pore defects. These defects, such as micropores, oxides, and inclusions, are challenging to completely eliminate, and corrosive gases can penetrate these defects and cause corrosion at the coating/substrate interface, leading to accelerated blistering and peeling of the coating.
To address these challenges, researchers have explored the use of relatively fine powders and high-speed coating processes, like HVOF (High-Velocity Oxy-Fuel) spraying, to improve the bond strength and durability of the coatings by reducing defects. In one study, Matsubara et al. applied HVOF-prepared NiCrSiB coatings on water-cooled walls in a high-efficiency boiler operating at 500 °C and 9.8 MPa. After two years of operation, no deterioration such as flaking was observed in the coating. The coating maintained good durability, and the highest corrosion rate observed was 50 μm/13800 h. The initial thickness of the coating was above 150 μm, suggesting a durability of about 6 years. The coating also demonstrated high corrosion resistance.
However, despite the advances made in minimizing defects using HVOF and other surface technologies, the defects of thermal spray coatings remain an ongoing concern. To further improve the performance of these coatings, researchers are developing remelting technology. This approach involves re-melting the lower melting point part of the coating using heat sources, leading to liquid phase penetration and diffusion that reduces or eliminates pores, cracks, and other defects. This results in a smoother coating morphology and improves the hardness, toughness, bonding strength, stress state, and overall performance of the coating.
The development of remelting technology is especially promising for equipment operating in harsh environments for extended periods. By enhancing the wear and corrosion resistance of the coating, remelting technology can expand the application range of thermal spray coatings and prolong their service life. As researchers continue to explore and refine these technologies, the reliability and performance of thermal spray coatings for waste incinerator boiler heating surfaces are expected to improve significantly.
In recent years, the application of high-frequency induction melting (NiCrBSi) alloy coating to water-cooled wall pipes has been successful. This coating exhibits several advantageous characteristics, including a uniform structure, strong metallurgical bonding with the substrate, a smooth surface, and a selectable thickness ranging from 0.5 to 2.5 mm, similar to traditional cladding layers. Compared to thermal spray coatings, this induction fusion coating boasts an exceptionally long service life with a corrosion rate almost equivalent to that of 625 alloy coatings. Depending on the specific corrosion conditions, it can be used for large water-cooled wall panels and superheaters of varying shapes.
One key advantage of the induction fusion coating is the establishment of a robust metallurgical bond at the interface, while effectively minimizing porosity, a common issue with conventional plasma, flame, and HVOF sprayed coatings. Additionally, the cost of tubes with induction fusion coatings is lower than those with overlay coatings, and the process minimizes product distortion, making the final assembly easier.
The test results have shown that the exposed surfaces of the induction fusion coating experience minimal corrosion, leading to increased boiler efficiency compared to using original fittings. On the contrary, pipes without this coating showed significant corrosion and thinning.
Another innovative coating technology, Cold Air Power Spraying (also known as Cold Spraying or Power Spraying), has emerged as the newest member of thermal spraying processes. This technology deposits coatings at temperatures lower than the melting point of the raw material powder particles, allowing the coating particles to retain their original properties even after the formation of the coating. Cold spraying achieves deposition efficiencies of over 90% and results in coatings with very low porosity.
Furthermore, Cold Air Power Spraying is considered a green technology due to its avoidance of flammable fuels or gases and its limited energy consumption as a low-temperature process. However, it currently lacks the widespread application and research interest achieved by other thermal spraying processes like plasma spraying and HVOF spraying, making it less commonly used in the industry.
For the anti-corrosion protection of water-cooled wall pipes, nickel-based alloys are commonly used as surfacing materials. One such example is Inconel 625 alloy, which is a high-strength high-temperature nickel-based alloy strengthened with Nb and Mo. It is capable of withstanding high-temperature and chlorine-based corrosion conditions. Through overlaying, a dense and thick coating with metallurgical bonding to the base material can be achieved.
Studies have shown positive results with the use of Inconel 625 alloy for surfacing. For instance, when MIG welding Inconel 625 alloy onto 20G water-cooled wall pipes, no cracks or porosity defects were observed, and the surfacing layer exhibited good fusion with the substrate. The surfacing layer demonstrated superior mechanical properties, including higher tensile strength, yield strength, elongation, and impact work compared to the 20G substrate. In real-world tests, when the alloy 625 surfacing layer was applied to the water-cooled wall of a 500 °C / 9.8 MPa high-efficiency garbage incinerator, the maximum corrosion rate observed was about 0.1 ~ 0.2 mm / year, and the durability of the alloy 625 surfacing layer was proven to be about 10 years.
However, surfacing also comes with some challenges. Repeated application in the same area may lead to embrittlement of the old cladding and cause crack extension into the cover pipe. The dilution of alloying elements, such as Fe, from the base material into the cladding layer can reduce its corrosion resistance. Moreover, the surface of the cladding layer is usually rough and uneven, which may accelerate corrosion due to increased slag adherence. The greater thickness and low thermal conductivity of the cladding layer can lead to an imbalance in the thermal distribution in the furnace chamber, causing thermal fatigue cracking of the coating. To address these issues, some researchers have proposed using cold metal transfer (CMT) laser welding technology for cladding. This technology allows for better control of the molten pool temperature, resulting in a lower dilution rate and a high-quality fusion cladding layer, making it a more promising welding technique.
2.1.3 Boiler heating surfaces
For the anti-corrosion protection of water-cooled wall pipes, nickel-based alloys are commonly used as surfacing materials. One such example is Inconel 625 alloy, which is a high-strength high-temperature nickel-based alloy strengthened with Nb and Mo. It is capable of withstanding high-temperature and chlorine-based corrosion conditions. Through overlaying, a dense and thick coating with metallurgical bonding to the base material can be achieved.

Studies have shown positive results with the use of Inconel 625 alloy for surfacing. For instance, when MIG welding Inconel 625 alloy onto 20G water-cooled wall pipes, no cracks or porosity defects were observed, and the surfacing layer exhibited good fusion with the substrate. The surfacing layer demonstrated superior mechanical properties, including higher tensile strength, yield strength, elongation, and impact work compared to the 20G substrate. In real-world tests, when the alloy 625 surfacing layer was applied to the water-cooled wall of a 500 °C / 9.8 MPa high-efficiency garbage incinerator, the maximum corrosion rate observed was about 0.1 ~ 0.2 mm / year, and the durability of the alloy 625 surfacing layer was proven to be about 10 years.
However, surfacing also comes with some challenges. Repeated application in the same area may lead to embrittlement of the old cladding and cause crack extension into the cover pipe. The dilution of alloying elements, such as Fe, from the base material into the cladding layer can reduce its corrosion resistance. Moreover, the surface of the cladding layer is usually rough and uneven, which may accelerate corrosion due to increased slag adherence. The greater thickness and low thermal conductivity of the cladding layer can lead to an imbalance in the thermal distribution in the furnace chamber, causing thermal fatigue cracking of the coating. To address these issues, some researchers have proposed using cold metal transfer (CMT) laser welding technology for cladding. This technology allows for better control of the molten pool temperature, resulting in a lower dilution rate and a high-quality fusion cladding layer, making it a more promising welding technique.
2.2 Superheater protection
Superheaters in waste incinerators operate at high steam temperatures ranging from 350°C to 500°C. The main cause of rapid degradation of superheater materials in waste incinerators is deposition-induced corrosion, where chlorides are deposited on the tubes. One effective strategy to mitigate corrosion in superheaters is through alloy modification. Conventional iron-based superheater alloys containing 1% to 2% Cr often experience rapid corrosion. However, high-alloyed steels, such as austenitic stainless steels or nickel-based alloys, have shown better corrosion resistance and are considered suitable candidates for superheater tubing or protective coatings.
Corrosion-resistant coatings are particularly important for superheater tubes operating at higher temperatures and in more severe corrosive environments. While austenitic stainless steels have good corrosion resistance, they are rarely used as coatings due to issues with weldability and mismatched coefficients of thermal expansion. Instead, various materials such as nickel-based alloys, metal-ceramic coatings, and ceramic coatings have been applied to protect waste incinerator superheater tubes. The choice of protective coatings depends on the corrosive conditions of different parts and the need to balance cost-effectiveness with performance.
2.2.1 Protection with Corrosion-Resistant Alloys
In the quest for safeguarding superheaters in waste incinerators against corrosion, researchers have conducted experiments to evaluate the thermal corrosion resistance of various materials. The study compared commonly used superheater materials, including ferritic steel 13CrMo44, ferritic-martensitic steel HCM12A, austenitic stainless steels Super 304, 317L, and Sanicro 28, as well as nickel-based alloys Hastelloy C-2000 and Inconel 625.
The results unveiled a significant disparity in corrosion rates and types of corrosion between the low-alloyed materials (13CrMo44, HCM12A, and Super 304) and the high-alloyed materials (317L, Sanicro 28, Hastelloy C-2000, and Inconel 625). The low-alloyed materials exhibited rapid and relatively uniform corrosion, with minimal positive impact from increased alloying. These alloys formed less protective metal chloride/oxide layers.
Conversely, the high-alloyed materials exhibited significantly more protective oxide layers. The presence of Ni and Mo in these materials inhibited the formation of metal chlorides and facilitated the development of Cr-rich oxide films. These oxide films possessed considerably lower fouling thicknesses compared to the low-alloyed materials, thereby enhancing their corrosion resistance.
To address cost concerns and reduce maintenance expenses, there has been a growing demand for cost-effective Ni-based alloys with high corrosion resistance. In response, Japan has developed high Si, high Cr, and high Ni alloys, namely MACN and MACF, respectively. These alloys lack Mo but demonstrate exceptional corrosion resistance in harsh compound corrosive environments involving chlorination, sulfidation, and oxidation reactions. Test results after 4 years of exposure in a high-efficiency waste incineration boiler at 500°C and 9.8 MPa indicated that both MACN and MACF alloys outperformed conventional alloy 625 in terms of corrosion resistance. The excellent corrosion resistance of these two alloys was attributed to the formation of protective Cr2O3 and SiO2 layers.
The development of corrosion-resistant alloys such as MACN and MACF shows promise in providing more cost-effective and durable protection for superheaters in waste incinerators. This advancement could lead to improved efficiency and reduced maintenance costs in waste incineration processes.
2.2.2 Metal-Ceramic Coating: Preparation and Application
Metal-ceramic composite coatings have emerged as a significant surface improvement technology, harnessing the remarkable properties of both metal and ceramic materials, such as high hardness, modulus of elasticity, abrasion resistance, thermal hardness, and compressive strength (up to 6000 MPa). These coatings have the capability to meet specific functional requirements, attracting increasing attention from materials researchers.

HVOF (High-Velocity Oxygen Fuel) is a widely used method to prepare metal-ceramic coatings that can effectively withstand thermal corrosion on heated surfaces in waste incinerators. Researchers like Fukuda et al. have successfully developed high-quality metal-ceramic coatings with strong adhesion to the substrate and low porosity using explosion spraying and HVOF processes. In laboratory experiments, they evaluated the corrosion resistance of various coatings.
Among these coatings, the 50%625-50%TiO2 metal-ceramic coating demonstrated superior corrosion resistance and was applied to the superheater tubes of a waste incinerator operating at 500 °C and 9.8 MPa. In comparison to corrosion-resistant alloy tubes like Alloy625, Alloy825, and SUS310J1, the 50%625-50%TiO2 coating exhibited excellent performance on secondary superheater tubes. Under the given corrosion conditions with a gas temperature of 488 °C and a metal temperature of 451 °C, the coating with a thickness of 200 mm showcased a lifespan of approximately 3 years.
However, it is essential to note that this coating experienced failure after just 2000 hours of corrosion on tertiary superheater tubes, where the flue gas temperature reached 620 °C, and the metal temperature was at 452 °C. The discrepancy in gas temperatures between the secondary and tertiary superheater positions indicated that gas temperature significantly influences the corrosion rate in these areas. Additionally, the experimental section located near the soot blower experienced accelerated corrosion due to the impact of steam ejected from the soot blower, which acted as another contributing factor to corrosion.
In conclusion, metal-ceramic coatings prepared through HVOF offer promising protection against thermal corrosion in waste incinerators, with excellent resistance to harsh conditions. Nevertheless, understanding the impact of gas temperature variations and other environmental factors is crucial in optimizing the performance and durability of these coatings.
2.2.3 Ceramic Coatings: Gradient Composite Coatings for Improved Corrosion Resistance
Ceramic coatings offer unique challenges due to the significant difference in thermal expansion coefficients between the ceramic coating and the base material. To address this issue, an intermediate transition layer is commonly employed to mitigate thermal expansion mismatch. The use of gradient composite coatings combines the abrasion resistance of the top layer with the corrosion resistance of the bottom layer, leading to a substantial improvement in the overall corrosion resistance of the coating.
In a study by Kawahara et al., three coatings—625/YSZ, NiCrSiB/YSZ (coated with a sealer), and NiCr/Cr3C2—were applied to the superheater of a waste incinerator to evaluate their corrosion resistance. The results showed that the predicted service life of the NiCr/Cr3C2coating, specifically at the steam inlet of the tertiary superheater, which experiences the most severe corrosive conditions, was 1.5 years. Meanwhile, the predicted service life of the unaffected part near the soot blower exceeded 3 years. This indicated a significant enhancement in the durability of Ni-based alloy/YSZ composite coatings compared to the NiCrSiB single-layer coating prepared by conventional supersonic flame, which only lasted a few months under similar corrosive conditions.
Table 2 presents the comprehensive evaluation results of the coatings’ durability after exposure for 1.3 years. The composite coatings demonstrated the ability to prevent substantial loss of tube wall thickness across various parts of the superheater, contributing to continuous plant operation and reduced maintenance costs. Comparing the durability of these coatings with the previously mentioned supersonic flame sprayed 50%625-50%TiO2 cermet coatings, it was found that the order of corrosion resistance, from strongest to weakest, was: 625/YSZ, NiCrSiB/YSZ, 50%625-50%TiO2, and NiCr/Cr3C2. This suggests that ceramic gradient composite coatings exhibit superior durability compared to metal-ceramic coatings. However, further verification is needed to establish the extent of this superiority, whether it is under normal or accidental operating conditions.
In conclusion, ceramic coatings with gradient composite structures show great promise in enhancing corrosion resistance in waste incinerator superheaters. By carefully selecting the composition and design of the coatings, researchers can achieve extended service life and better protect the critical components of waste incineration plants.
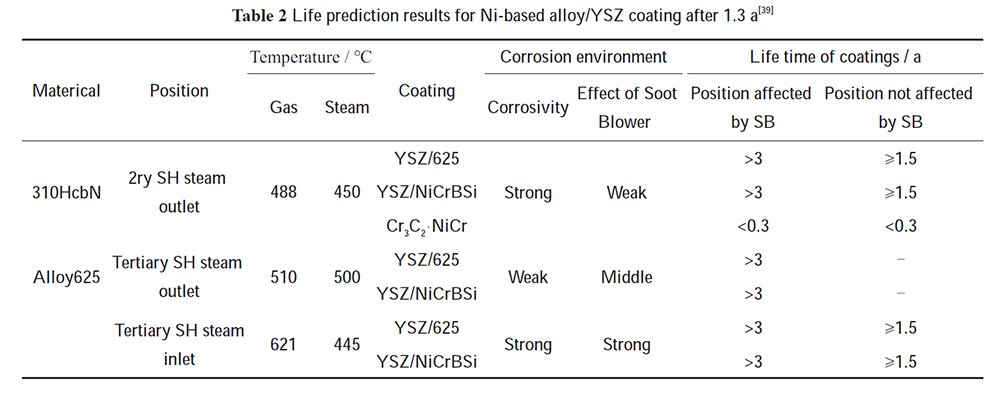
2.2.4 Laser Cladding: Corrosion Resistance for Critical Components in Waste Incinerators
Laser cladding offers several advantages over conventional MIG cladding, including low dilution, a wide range of material selection, controllable heat input, thin coating thickness, and excellent abrasion resistance. As a result, laser-clad tubes and large panels are increasingly being installed in operational boilers. CESIRicerca’s laser cladding equipment, capable of producing high-quality cladding layers with thicknesses ranging from 0.7 to 1 mm and minimal dilution of the base material, has paved the way for corrosion resistance investigations in municipal waste incinerator plants.
Fantini conducted extensive field experiments on the corrosion resistance of 625 alloy laser cladding, applied to critical components in waste incinerators, across several plants in Italy and Europe. The 625 alloy laser cladding, with an initial thickness of 1 mm ± 7%, exhibited average corrosion rates of 0.15 and 0.18 mm/a after 15,560 and 11,650 hours in MSB and GKS superheaters, respectively (corrosion temperatures of 420 and 435 °C, respectively). Additionally, the average corrosion rate was approximately 0.5 and 0.8 mm/a in the NRB plant after 14,700 hours of 625 alloy laser cladding at 440 °C. On MSB and GKS superheaters, the average corrosion rate was about 1.5 mm/a. However, the researchers noted that the corrosion resistance of the 625 alloy laser cladding significantly deteriorated at temperatures exceeding 500 °C.
Another study by Liu et al. utilized the weightlessness method to investigate the corrosion resistance of TP347H, C22 alloy, and laser cladding C22 coatings in molten chlorine salts at temperatures ranging from 450 to 750 °C. Their findings revealed that the laser-coated C22 coating exhibited the most excellent corrosion resistance, followed by C22 alloy, while TP347H had the least resistance.
Researchers concluded that in biomass power plants, where superheater tubes typically experience surface temperatures of 400 to 750 °C, and localized superheating may push tube surface temperatures above 750 °C, laser-melting coated C22 coatings proved effective in preventing corrosion of superheater tubes under such operating conditions. The corrosion-resistant properties of laser cladding make it a promising technology for protecting critical components in waste incinerators, extending their service life and reducing maintenance costs.
In conclusion, corrosion protection in waste incinerators and power plants is a critical aspect to ensure the durability and efficiency of equipment. Highly alloyed materials with good corrosion resistance are desirable, but their use can be limited due to stringent regulations, high costs, and technical complexities. To address these challenges, the application of low-cost alloyed steels coated with highly corrosion-resistant coatings has emerged as an attractive and cost-effective solution.
Advancements in coating preparation technologies have shown promising results in recent years, enabling the development of coatings with improved properties and reduced defects. Unique coating processes, such as small-diameter pipeline coating, on-site coating for boiler components, and repair of worn coatings, have provided new business opportunities for boiler protection. However, certain scientific and technical challenges still need to be addressed, such as porosity, flake boundaries, bond strength, cohesion, surface quality, and residual stress, which can impact the overall coating quality and durability.
Future research and development efforts should focus on enhancing coating properties, reducing the production cost of metal powders, and making coating equipment more accessible. By overcoming these challenges, corrosion protection technologies can play a vital role in extending the service life of equipment and reducing maintenance costs for waste incinerators and power plants.
[Source] QU Zuopeng, ZHANG Beibei, XIE Guangxiao, YANG Yuxi, WANG Yongtian, TIAN Xinli,WANG Haijun, Journal of Chinese Society for Corrosion and Protection, 1005-4537(2023)03-0452-08
DHB Boiler
Discover The Superior Quality And Cutting-Edge Technology Of DHB Boilers. Explore Our Range Of Biomass Boilers, Waste Heat Boilers, And More. Take Your Industrial Operations To New Heights With DHB Boiler.