1. Understanding the Primary Role of a Coal Economizer
At the heart of industrial boiler optimization, the coal economizer assumes a pivotal role, strategically designed to elevate thermal efficiency and mitigate energy consumption. Its significance is underscored by the meticulous process of capturing and utilizing waste heat emanating from the boiler exhaust, a mechanism intricately aligned with the overarching goals of energy conservation and emission reduction.
Enhancing Thermal Efficiency: The primary mission of the coal economizer is to act as a catalyst for heightened thermal efficiency within the boiler system. By efficiently capturing and repurposing waste heat, the economizer contributes to a more effective utilization of energy resources, ensuring that each unit of fuel generates maximal output.
Mitigating Energy Consumption: Beyond its efficiency-enhancing capabilities, the coal economizer plays a crucial role in the broader strategy of energy conservation. By harnessing and repurposing otherwise wasted heat energy, it aids in the reduction of overall energy consumption, fostering a sustainable approach to industrial processes.
Strategic Waste Heat Utilization: The mechanism by which the coal economizer achieves its objectives involves the strategic utilization of waste heat present in the boiler exhaust. This waste heat, which would otherwise dissipate into the environment, is harnessed and redirected for practical purposes, aligning with contemporary imperatives for sustainable and eco-friendly industrial practices.
In essence, the coal economizer emerges as a key player in the pursuit of operational efficiency and environmental responsibility within industrial settings. Its role extends beyond mere functionality, embodying a commitment to the dual objectives of optimizing resource utilization and contributing to a greener, more sustainable industrial landscape.

2. Diverse Classifications of Coal Economizers
In the realm of coal economizers, they undergo diverse categorizations based on distinct parameters:
Positional Classification: There are two primary categories based on position—front smoke chamber economizers and tail smoke chamber economizers. These placements play a pivotal role in determining the efficiency and functionality of the economizer within the broader boiler system.
Fluid Nature Differentiation: Coal economizers are also classified based on the fluid they interact with. This classification gives rise to two main types—water economizers and air economizers. The nature of the fluid involved significantly influences the economizer’s performance and its ability to harness waste heat effectively.
Structural Diversity: Further categorization arises from the structural composition of coal economizers. They come in various forms such as coil type, fin type, spiral type, among others. Each structural type is designed with specific considerations, impacting heat transfer efficiency and overall adaptability to diverse boiler configurations.
Understanding these classifications is pivotal for selecting the most suitable coal economizer configuration, tailored to the unique requirements of different industrial settings.
3. Impact of Coal Economizer Outlet Water Temperature
A noteworthy point is that with each 1℃ increase in the coal economizer outlet water temperature, there is an approximate 1℃ decrease in the average boiler exhaust temperature.
4. Strategic Installation of Economizers
When it comes to the strategic installation of economizers, a meticulous approach is paramount for ensuring peak performance within a boiler system. Generally, economizers find their designated place upstream in the boiler exhaust flue, positioned strategically between the combustion chamber and the air preheater.
Strategic Positioning Upstream: The placement of economizers upstream is a deliberate choice, carefully selected to capitalize on the flow dynamics within the boiler system. By situating the economizer in this position, it intercepts the hot gases at their earliest point of exit, optimizing the capture of waste heat before it dissipates into the environment.
Between Combustion Chamber and Air Preheater: Within this carefully selected location, economizers take their place between the combustion chamber and the air preheater. This placement is tactically chosen to facilitate the extraction of heat from the flue gases, a critical step in the process of energy recovery. The combustion chamber represents the point of origin for these gases, and the air preheater lies downstream, preparing the incoming combustion air. Placing the economizer in this intermediary position allows for the effective utilization of waste heat to enhance the overall thermal efficiency of the boiler.
In essence, the strategic installation of economizers serves as a linchpin in the quest for operational excellence. By thoughtfully placing these devices in the optimal position within the boiler system, industries can harness the full potential of waste heat recovery, contributing to both energy efficiency and environmental responsibility.
5. Advantages of Utilizing a Coal Economizer
The integration of a coal economizer into an industrial boiler system yields a myriad of advantages, significantly influencing operational efficiency, environmental impact, and equipment longevity.
Enhanced Thermal Efficiency and Fuel Economy: A primary advantage lies in the notable improvement of thermal efficiency achieved through the use of a coal economizer. By capturing and repurposing waste heat from the boiler exhaust, the economizer facilitates a more efficient utilization of energy resources. This translates into enhanced heat transfer efficiency, ensuring that each unit of fuel contributes more effectively to the overall heating process. As a result, industries experience a tangible reduction in fuel consumption, optimizing resource utilization and operational costs.
Emission Reduction for Environmental Well-being: The incorporation of a coal economizer plays a pivotal role in reducing emissions, thereby mitigating environmental pollution. The economizer’s ability to harness waste heat not only enhances efficiency but also minimizes the release of harmful pollutants into the atmosphere. This dual impact fosters a greener industrial footprint, aligning with contemporary sustainability goals and regulatory requirements. Lowered emissions contribute significantly to environmental conservation, making the economizer a key player in responsible industrial practices.
Prolonged Boiler Lifespan: Beyond efficiency gains and environmental benefits, the utilization of a coal economizer extends the operational lifespan of the boiler. By optimizing the thermal conditions and reducing the strain on components, the economizer helps mitigate wear and tear. This, in turn, translates into less frequent maintenance requirements and a prolonged overall lifespan for the boiler system. The economizer acts as a protective measure, ensuring sustained reliability and performance over an extended period.
In essence, the advantages of incorporating a coal economizer extend far beyond immediate efficiency gains. They encompass a holistic approach to industrial operations, encompassing economic benefits, environmental responsibility, and the preservation of valuable equipment assets.
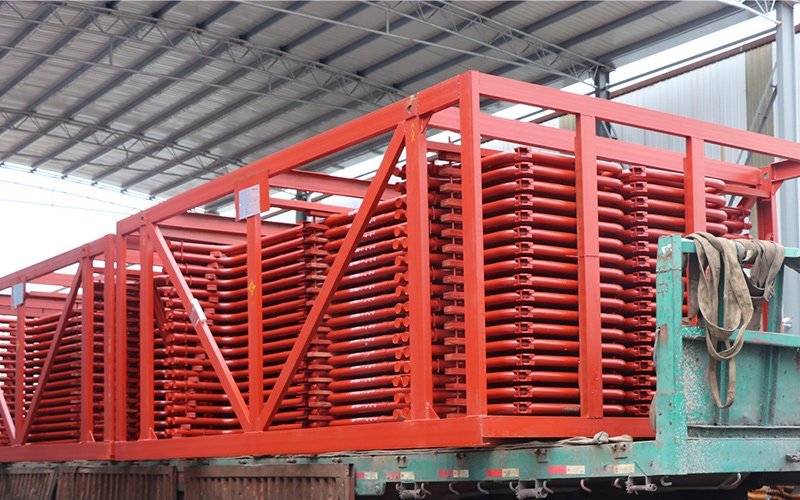
6. Challenges and Considerations in Coal Economizer Implementation
The implementation of coal economizers, while offering substantial benefits, comes with its set of challenges and considerations that necessitate careful attention within industrial settings.
Elevated Installation and Maintenance Costs: One notable challenge in the deployment of coal economizers is the higher associated installation and maintenance costs. The intricate nature of these systems, coupled with the need for precision in installation, contributes to an initial investment that may be comparatively higher. Additionally, ongoing maintenance demands attention to ensure consistent and optimal performance. Industries contemplating the adoption of coal economizers need to weigh these upfront and recurring costs against the anticipated long-term efficiency gains.
Susceptibility to Flue Gas Corrosion and Ash Buildup: Coal economizers are susceptible to the corrosive effects of flue gas and the accumulation of ash. The corrosive nature of flue gases can degrade the economizer components over time, necessitating vigilant monitoring and protective measures. Ash buildup poses an additional concern, potentially impeding heat exchange efficiency. Regular inspections and cleaning routines are imperative to mitigate these challenges, ensuring the economizer’s sustained functionality.
Sensitivity to Sulfuric Acid and Moisture in Flue Gas: Another consideration is the sensitivity of coal economizers to sulfuric acid and moisture present in flue gases. Exposure to these elements can accelerate corrosion and compromise the structural integrity of the economizer. Implementing measures to address sulfuric acid and moisture content becomes crucial to prolong the lifespan of the economizer and maintain its effectiveness in waste heat recovery.
In summary, while coal economizers offer significant advantages, a nuanced approach is required to address the challenges and considerations associated with their implementation. Vigilant planning, proactive maintenance, and protective measures are indispensable for maximizing the long-term benefits of these systems in industrial applications.
7. Factors Guiding Selection and Design
Considerations include boiler operating parameters, exhaust gas characteristics, water quality requirements, and available installation space.
8. Operational Tips and Maintenance Guidelines
To ensure the continuous and effective performance of coal economizers, implementing diligent operational tips and adhering to maintenance guidelines is paramount. Here’s a comprehensive expansion on key practices:
1. Regular Ash Accumulation Cleaning for Scaling and Corrosion Prevention: A crucial step in maintaining the operational efficiency of coal economizers involves the systematic cleaning of ash accumulation. Regular removal of ash prevents the formation of scale, which could impede the heat exchange process and compromise the structural integrity of the economizer. This preventative measure not only safeguards against scaling issues but also mitigates the risk of corrosion, extending the lifespan of the economizer and sustaining its optimal functionality.
2. Continuous Monitoring of Water Quality to Mitigate Corrosion and Scaling Issues: Vigilant monitoring of water quality is essential for averting corrosion and scaling problems within the coal economizer. Water impurities can contribute to the degradation of components and reduce heat transfer efficiency. By maintaining stringent control over water quality, industries can proactively address potential issues, preserving the economizer’s performance and minimizing the need for extensive maintenance. Regular water quality assessments and appropriate corrective measures constitute integral components of a comprehensive maintenance strategy.
3. Periodic Inspection of Sealing and Connections: Ensuring the integrity of sealing and connections is fundamental to the reliable operation of the coal economizer. Periodic inspections should be conducted to identify any signs of wear, leaks, or degradation in seals and connections. Addressing these issues promptly prevents energy loss and maintains the airtight integrity of the system. This routine examination contributes significantly to the economizer’s longevity and sustained efficiency in capturing and utilizing waste heat.
By conscientiously incorporating these operational tips and maintenance guidelines into industrial practices, businesses can optimize the performance of their coal economizers, thereby realizing the full spectrum of benefits associated with energy efficiency and environmental responsibility.
9. Evaluation of Energy Saving Effects
The effectiveness of energy savings can be gauged by improvements in thermal efficiency and reductions in fuel consumption. Generally, the installation of a coal economizer substantially boosts boiler thermal efficiency, achieving the goal of energy conservation.
DHB Boiler
Discover The Superior Quality And Cutting-Edge Technology Of DHB Boilers. Explore Our Range Of Biomass Boilers, Waste Heat Boilers, And More. Take Your Industrial Operations To New Heights With DHB Boiler.