In the pursuit of enhanced energy efficiency and emissions reduction at Guixi Smelter, a comprehensive study has been conducted to improve and optimize the steam dryer hydrophobic recovery system. The primary objectives include aligning the hydrophobic recovery system with actual process requirements, mitigating operational labor intensity, and reducing error rates. This initiative focuses on addressing the complexities associated with the operation and shutdown of the steam dryer under various production conditions. Differentiated discharge and recycling methods for hydrophobic water are implemented, accompanied by a shift from manual adjustments to automated valve control. This strategic transformation aims to elevate the system’s intelligence, diminishing the need for extensive human intervention. Through practical operation, statistical investigations, and analysis, it becomes evident that the intelligent automation of the hydrophobic recovery system significantly influences its stable operation.
Maximizing Efficiency in Waste Heat Boiler Systems
Steam, a versatile heat carrier employed across diverse industries, undergoes indirect or direct heating processes, releasing latent heat of vaporization upon temperature reduction. A portion of this energy transforms into steam condensate, manifested as hydrophobic water discharged from the system. Research indicates that this hydrophobic steam energy constitutes 20% to 50% of the thermal energy, offering high-temperature advantages with quality water that requires no softening. This presents a pivotal breakthrough for modern factories, enabling cost savings and reduced energy consumption. Without proper recycling treatment, direct discharge of hydrophobic water results in considerable waste and environmental pollution, including high-grade water wastage, smoke emissions, excessive noise, and ring pollution.
Towards Sustainable Thermal Recycling
To optimize the entire plant’s steam heat source and achieve thermal recycling economy goals, a structured approach is adopted. The hydrophobic water from the steam dryer in the melting workshop undergoes recovery processes, being directed to the power workshop’s deaerator. After deaeration, the recovered water is efficiently conveyed to the designated boiler through a feed pump. This systematic recycling of waste heat ensures the effective utilization of the steam heat source, contributing to a sustainable and economically viable thermal recycling system.
Overview of Steam Dryer Water Recovery Systems
The current landscape of steam dryer water recovery devices is contingent on two distinct recycling methods: open and closed systems. The choice between the two hinges on whether the hydrophobic recovery system is directly connected to the atmosphere. To enhance energy efficiency and minimize heat loss, a prevalent approach in power centers is the adoption of closed systems. In these configurations, hydrophobic water either undergoes direct recycling through a heat exchanger or is routed to a closed softened water tank for production water. Alternatively, the hydrophobic water may be channeled to the deaerator for makeup water and steam heating. Notably, the steam dryer’s hydrophobic recovery stands out as a key project within the broader energy-saving and emission reduction initiatives of the plant, employing the latter method to directly recycle hydrophobic water to the deaerator. This not only conserves energy, including softened water and steam but also facilitates the substantial recycling of waste heat.
Role of Power Deaerator in Water Treatment
The power deaerator, a critical component utilizing thermal deoxygenation, serves as essential support equipment for boilers such as flash furnaces and converters. Its primary function is to provide boiler feed water in line with production requirements while playing a crucial role in the boiler water system. Operating through the heating of steam and reverse osmosis treatment of softened water, the power deaerator effectively reduces the oxygen content in the water. This process ensures that the water supplied to the boiler adheres to the necessary indicators, preventing high-temperature oxidative corrosion of metal components within the boiler system.
Significance of Steam Dryer in Waste Heat Generation
The steam dryer is a pivotal element in the flash furnace melting process, generating a substantial amount of high-temperature waste heat. Utilizing saturated steam at 1.4 MPa pressure, the steam dryer efficiently pre-dries copper concentrate with a moisture content of 8% to 10%, ultimately reducing it to less than or equal to 0.3%. During operation, saturated steam exchanges heat with the copper ore powder and is discharged as hydrophobic water from the dryer. On-site assessments reveal the discharged hydrophobic water’s temperature reaching 135 ℃, with a volume of approximately 30 t/h and a nearly neutral pH. This hydrophobic water proves to be a viable substitute for the softened water required by the deaerator in actual production. It boasts direct heat energy recovery and utilization capabilities, motivating the plant to incorporate steam drying hydrophobic water recycling to enhance the overall utilization of steam heat energy.
Steam Drying Hydrophobic Water Recovery Process Flow
The recovery process flow, depicted in Figure 1, elucidates the journey of hydrophobic water from the steam dryer to the deaerator and beyond. Saturated steam, sourced from the turbine generator post-power generation, is employed to heat moisture-laden mineral materials in the steam dryer. The released latent heat of vaporization transforms the steam into saturated condensate, maintaining nearly identical temperature and pressure. The condensate is then discharged from the steam dryer, propelled by rotor centrifugal force and steam pressure. This discharged condensate travels to the power center and, after depressurization in the expansion vessel, proceeds to the 0.1 MPa deaerator. Here, it produces a significant amount of secondary flash steam and condensate, serving as supplemental water and heating steam for the deaerator. Ultimately, the recovered water, facilitated by a feed pump, reaches waste heat boilers, such as those in flash furnaces and converters, generating steam for turbine generator power generation, completing the thermal cycle of the entire steam dryer hydrophobic recovery system.

Achievements and Challenges in Steam Dryer Hydrophobic Recovery
The successful implementation of steam dryer hydrophobic recovery, recovering and utilizing approximately 30 t/h of condensate, has indeed realized significant energy savings and emission reduction goals. The deaerator’s heating steam consumption is nearly zero, yielding substantial socio-economic benefits for the plant and conserving up to 720 t of water resources daily. However, the subsequent operational period has unearthed certain adverse effects on the stable and safe operation of the entire process system.
Operational Challenges and Adverse Impacts
Post-implementation, it became evident that the steam dryer hydrophobic recovery system introduced certain challenges. Firstly, the deaerator experienced an average of 5 to 6 occurrences per month where temperature and pressure spiked suddenly. This led to feed pump cavitation, posing serious safety risks and destabilizing the boiler water system, thereby compromising subsequent waste heat boiler operations. Secondly, the hydrophobic recovery system introduced intermittent acidic pH levels in the boiler feed water, contrary to safety requirements, further jeopardizing the waste heat boiler’s secure operation.
Investigating pH Discrepancies
To address the issue of acidic boiler feed water, a comprehensive pH analysis was conducted on the boiler feed water, steam dryer trap water, and softened water. Results indicated that the pH of softened water remained stable and neutral at approximately 7~8, eliminating it as a contributing factor. However, the pH of steam dryer trap water exhibited significant fluctuations, occasionally reaching acidic levels of 3~4, substantially impacting the pH of the boiler feed water.
Identifying Root Causes
In-depth data comparison and analysis focused on factors such as deaerator heating steam volume, deaerator water volume, boiler feed water volume, and steam dryer sparge water volume. The findings highlighted that fluctuations in pressure and temperature were primarily influenced by the steam dryer sparge water volume and boiler feed water volume. This understanding provided crucial insights into the operational challenges faced by the system.
Root Causes: Working Conditions of Steam Dryer
Upon extensive investigation, it was concluded that the aforementioned problems stemmed mainly from the varying working conditions during the operation and shutdown of the flash furnace steam dryer. The high-temperature and high-pressure environment during prolonged operation posed a risk of steam coil rupture. Consequently, during maintenance, copper concentrate powder inadvertently leaked into the steam coil. Upon re-entering operation, this leakage, combined with hydrophobic water, impacted the pH levels, affecting both boiler feed water and waste heat boiler stability. Simultaneously, the interplay between the operation and shutdown of the steam dryer influenced the water volumes in the flash furnace boiler and steam dryer, causing fluctuations in deaerator water temperature and pressure. In severe cases, this fluctuation could lead to cavitation in the waste heat boiler’s feed pump, further compromising safety. Addressing these root causes is imperative to ensure the continued success of the steam dryer hydrophobic recovery system.
Optimizing Steam Drying Hydrophobic Water Recovery
2.1 Transformation Ideas for Steam Drying Hydrophobic Water Recycling System
Following a thorough investigation and analysis, coupled with insights from post-implementation operations, optimizations were identified for the existing challenges. First, to address the issue of prolonged high temperature and pressure in the deaerator, leading to waste heat boiler feed pump cavitation, a sewage valve was customarily opened at the bottom of the deaerator for mandatory water exchange. However, this method resulted in resource waste, environmental pollution, and challenges in controlling deaerator level fluctuations. Research suggests introducing a new bypass to the softened water tank in the steam dryer trap piping. The bypass, controlled by a pneumatic valve connected to the deaerator pressure, ensures automatic decompression and shunting of steam dryer trap water to the softened water tank. This not only avoids cavitation but also enhances heat exchange, raising the deaerator water temperature.
Secondly, during furnace shutdown or maintenance, acidic concentrate powder mixed with steam drying trap water enters the recycling pipeline, disrupting the pH of the water. To address this, a new bypass was added to the steam dryer drain recovery piping, utilizing flash furnace steam dryer drain and adding it before entering the power deaerator. This method prevents direct discharge from the flash furnace, avoiding safety risks due to sudden high-temperature hydrophobic water impact. Additionally, considering the heat energy in the hydrophobic water, a heat exchanger on the softened water in the softened water tank was introduced for heat transfer, minimizing heat energy waste during external discharge.
2.2 Optimization Program for Steam Drying Recovery System
While ensuring the normal recovery and utilization of steam drying water, two successive renovations were undertaken to address the need for discharge during furnace shutdown and overhaul. The first modification focused on ensuring the safety of steam dryer wastewater discharge and preventing deaerator level fluctuations and low pH in boiler feed water.
As depicted in Fig. 2, the first modification involved adding recovery valves and a bypass as a drain on the gas and water balance pipes connecting the hydrophobic recovery system to the deaerator. Manual switching was required during external recovery operations, posing challenges in valve sequence and operating experience. Incorrect valve switching could result in deaerator pressure issues and water discharge anomalies. However, this modification proved less than satisfactory, prompting a second optimization.
In the second optimization, efforts were made to reduce human error, enhance waste heat recovery utilization, and address high temperature and pressure in the deaerator. Further details of this optimization are presented in the subsequent section.
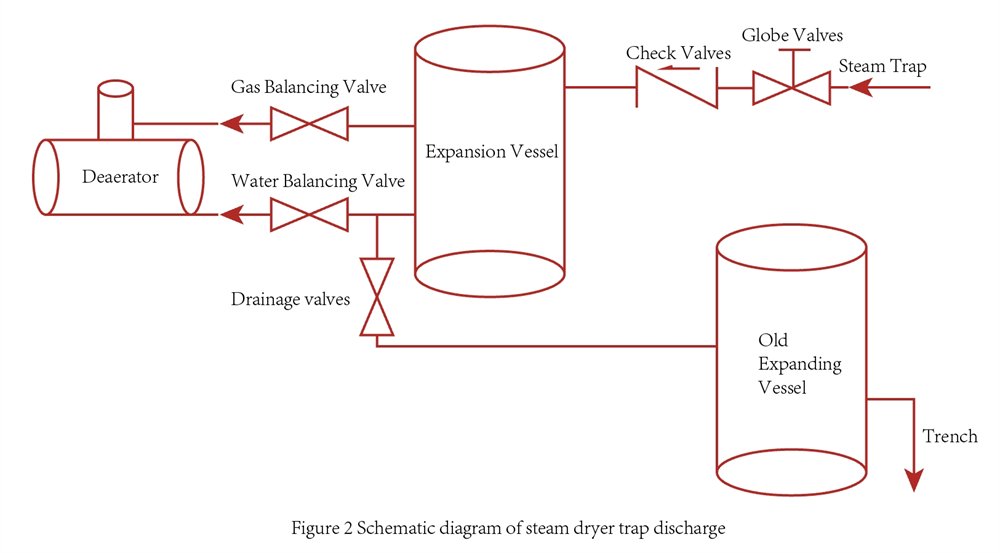
Optimizing Steam Drying Hydrophobic Water Recovery: Automated System Enhancement
In the second phase of system optimization, the primary objective was to address the recurrent issue of high temperature and high pressure in the deaerator. Automation was emphasized to reduce human influence and enhance operational efficiency. As illustrated in Figure 3, the optimization of the trap recovery system involved the installation of additional components such as heat exchangers, shut-off valves, check valves, and pneumatic valves. Additionally, new discharge piping was introduced before entering the expansion vessel, along with steam drying trap bypass piping connected to the softened water tank on the original steam drying trap piping entering the expansion vessel.
To streamline operations and enhance automation, a control program was implemented for the new trap discharge piping. Pneumatic valves 1 and 2 were added outside the expansion tank, along with pneumatic valve 3 on the new steam drying trap bypass pipe, creating interlocking mechanisms. Under normal steam drying trap recovery conditions, the trap enters the expansion vessel and eventually reaches the deaerator through the vapor balance pipe, completing the vapor recycling. If the deaerator pressure exceeds the set value, pneumatic valve 3 above the softened water tank automatically opens, diverting the steam drying traps through the bypass piping to the softened water tank. This stabilizes pressure and temperature, preventing excessive levels in the deaerator. The softened water tank’s robust buffering capacity efficiently absorbs and utilizes the heat from the bypassed dryer traps.
When discharging steam drying traps, opening pneumatic valve 1 on the newly added discharge piping via the DCS initiates the process. Pneumatic valve 2 into the expansion vessel is automatically closed. The steam drying traps are then regulated through valve 1, entering the softened water tank after pressure reduction in the expansion vessel. Subsequently, the traps are discharged into the ground ditch through a heat exchanger added to the water tank. The inclusion of check valves and differential pressure mechanisms minimizes pressure and water level fluctuations in the deaerator, ensuring the safety of the feedwater.

Conclusion
Following a period of practical implementation, the optimized steam drying hydrophobic recovery and utilization system is operating effectively. The addition of heat exchangers successfully reduced the discharge hydrophobic temperature from the original 135 ℃ to approximately 40 ℃, mitigating thermal pollution associated with steam drying hydrophobic discharge. Through thorough investigation and statistical analysis, it was observed that the optimization of the deaerator significantly reduced instances of overpressure and over-temperature, from the original 6 times per month to 0 times per month. The optimization also ensured the pH of boiler feed water, offering a comprehensive solution to issues arising from hydrophobic water recovery, particularly during dryer shutdowns or overhauls. This achievement contributes to the safety and seamless operation of the deaerator, generating economic benefits and cost savings.
Upon further investigation and statistics, each discharge of steam dryer hydrophobic water amounts to approximately 200 t, occurring at least 60 times a year. With the implementation of the recycling system, these discharges equate to the recovery of about 1,500 t of steam annually. Considering the current market price of steam at 240 yuan per ton, the annual cost savings from hydrophobic discharge alone amount to 360,000 yuan.
In summary, this optimization and transformation successfully achieved its intended goals, demonstrating a seamless integration without compromising the safe and stable operation of the original process. Furthermore, it has laid the groundwork for the future realization of an intelligent plant, showcasing the potential for continued advancements in operational efficiency and sustainability.
DHB Boiler
Discover The Superior Quality And Cutting-Edge Technology Of DHB Boilers. Explore Our Range Of Biomass Boilers, Waste Heat Boilers, And More. Take Your Industrial Operations To New Heights With DHB Boiler.