Through the study and practice of the large module lifting technology for NE waste heat boilers supporting 1500MW gas turbine power stations internationally, experiences and deficiencies are summarized, and the lifting technology for this type of waste heat boiler large modules is improved, providing positive references for similar future projects.
In recent years, with the benefits of the “Belt and Road” initiative, Chinese infrastructure enterprises have targeted the study of foreign equipment installation technology, which is of great significance for international engineering.
I. Introduction to the Waste Heat Boiler
Manufacturer: Italian NOOTER/ERIKSEN
Technical Features: The 1500MW gas turbine power station is equipped with 2 sets of waste heat boilers, which are three-pressure, reheating, non-auxiliary combustion, and natural circulation horizontal waste heat boilers. Each boiler has 16 modules arranged vertically (the heaviest is 265t, the lightest is 76t).
Parameters: Main steam: Flow rate 480.75t/h, Pressure 16.6Mpa, Temperature 587.4℃; Reheated steam flow rate 544.87t/h, Pressure 34.91bar, Temperature 586.2℃; Low-pressure steam: Flow rate 66.75t/h, Pressure 4.14bar, Temperature 318.6℃.
Lifting Technology Introduction: Each boiler is lifted on the north and south sides, using a 750t crawler crane for lifting, and a 500t crawler crane is used for lifting and unloading assistance. When the module turns 90° vertically, the 750t crawler crane lifts the module, and the turning frame is assisted by a 180t or 80t crawler crane with a 500t crawler crane to prevent tilting. When the module passes over the top of the turning frame, it is slowly placed on the ground.
II. Research on the Arrival Order of Large Modules
(1) Module Layout
The layout of the waste heat boiler large modules is shown in Figure 1.

(2) Waste Heat Boiler Modules
A1 (76t) \ B1 (76t) \ A2 (265t) \ B2 (265t) \ B3 (245t) \ B4 (248t) \ A3 (245t) \ A4 (248t);
C1 (76t) \ D1 (76t) \ C2 (265t) \ D2 (265t) \ C3 (245t) \ C4 (248t) \ D3 (245t) \ D4B4 (248t).
(3) Unloading Path
According to the actual situation, the modules can be delivered by reversing in or entering directly.
III. Machinery Required for the Process
(1) Large Machinery
- One 750t crawler crane (main arm 79.2m, super lift 390t);
- One 500t crawler crane (main arm 48m, super lift counterweight 250t);
- One 180t or 250t crawler crane (main arm 50m);
- One 80t crawler crane (main arm 40m);
- Two 50t truck cranes;
- One 10t forklift;
- One 40m access lift.
(2) Special Tools
- The manufacturer provides a special turning frame, 28,110mm in length and 5,604mm in width, weighing 44.04t, as shown in [2] Figure 2.

IV. Lifting Process Research
(1) Process Flow Planning
- Positioning and acceptance of the support frame marking – internal plant transportation – unloading and inspection upon arrival – lifting and turning, and positioning in place.
(2) Positioning and Acceptance of the Support Frame Marking
- Before the module is positioned, the positioning and marking of the support frame are required, including the distance, diagonal, and positioning blocks to ensure the smooth positioning of the module lifting.
(3) Internal Plant Transportation Study
- Taking the largest module #2 as an example, the inner diameter of the turning radius of the transportation vehicle is 13,450mm, and the outer diameter is 25,400mm, as shown in Figure 3.
- The total length of the module transportation vehicle is 53,320mm, with a platform length of 33,000mm, a vehicle width of 3,000mm, an equipment width of 4,036mm, and an overall height of 5,475mm.
- All modules are driven from the fixed end of the #1 waste heat boiler to the outside of the chimney road, then reversed into the bypass chimney section, with a total of 3 turning road sections for the two waste heat boiler modules, and then reversed into the unloading and lifting position.

(4) Unloading Process Study
- The module is transported to the designated unloading position and then lifted by a 500t (main arm 48m) and a 750t crawler crane (main arm 79.2m) and placed on the module unloading frame. After lifting, the module is connected with a lifting shackle and then lifted synchronously and placed above the turning frame.
- Module #1 Unloading Process Verification
- When lifting the unloading module, the lifting capacity of the crane is evenly distributed. The module unloading and lifting frame is 28t (including rigging), and the module weight is 76t. Therefore, the maximum unloading weight is 76+28=104t. The two cranes share the load evenly, with 104/2=52t each. The 500t crawler crane and 750t crawler crane do not add super-lift counterweights.
- Modules #2, #3, #4 Unloading Process Verification
- The heaviest module #2 is selected for study.
- Inspection
- Before unloading, an external inspection should be carried out, including dimensions, welds, deformations, lifting ears, numbers, and various pipe fittings, etc., to ensure that the unloading and lifting are error-free.
(5) Module Turning Process Study
- Each boiler module is lifted on both sides at the site, with boiler #1 lifting sides A and B first, then C and D, and boiler #2 lifting sides C and D first, then A and B.
- A special turning lifting frame is used.
- The 500t crawler crane lifts the turning frame, and the 750t crawler crane (with super-lift) lifts the module lifting ear. Then the 500t crawler crane (with super-lift) lifts the module alone, and the 750t crawler crane also rises slowly. The 500t crawler crane bears a load of 265t+44t=309t (the lifting point is basically at the center of the module’s center of gravity, 120mm forward), and there will be a slight tilt. It can be safely turned.
(6) Module Lifting Process Study
- Modules #1, #2, #3, and #4 weigh 76t, 265t, 245t, and 248t, respectively. Module #2 is used as an example for lifting study:
- Lifting elements for module #2: The weight of the lifted object is 265t, the crane hook is 11t, the rigging is 2t, the turning frame is 44t, and the 500t and 750t crawler cranes cooperate to lift and turn into place.
- When lifting and turning, the 500t crawler crane (SSL with super-lift, 16m radius, counterweight 250t) can calculate the lifting radius up to 14m, with a lifting capacity of 413t. The lifting load weight is 322t. When lifting and turning, the load rate of the 500t crawler crane is 322/413=78%, which meets the lifting requirements.
- When lifting and turning, the 750t crawler crane (with super-lift, 18m radius, counterweight 391.8t) can basically ignore the force when lifting and turning. The center of gravity of the equipment is at the center of the lifting point of the 500t crawler crane. Therefore, when the module turns to about 45°, the force on the 750t crawler crane will gradually increase. According to the principle of torque balance, the equipment and turning frame weigh 309t, and the force on the 750t crawler crane is about 46t, while the force on the 500t crawler crane is 263t.
- As long as the 750t ensures that the lifting radius is within 24m, it can meet the lifting requirements. When the 750t crawler crane has a lifting radius of 24m, the lifting capacity is 364.8t, and the lifting load weight is 278t (object + hook + rigging). The load rate of the 750t crawler crane is [1]278/364.8=76.2%, which meets the lifting requirements.
(7) Lifting Order Planning
- The AB row modules are lifted and positioned normally [3] from axis 2 to axis 8 in sequence. The process can be adjusted according to the actual situation of the equipment arrival, and the order is shown in Figure 4 (#1, #2, #3, #4).
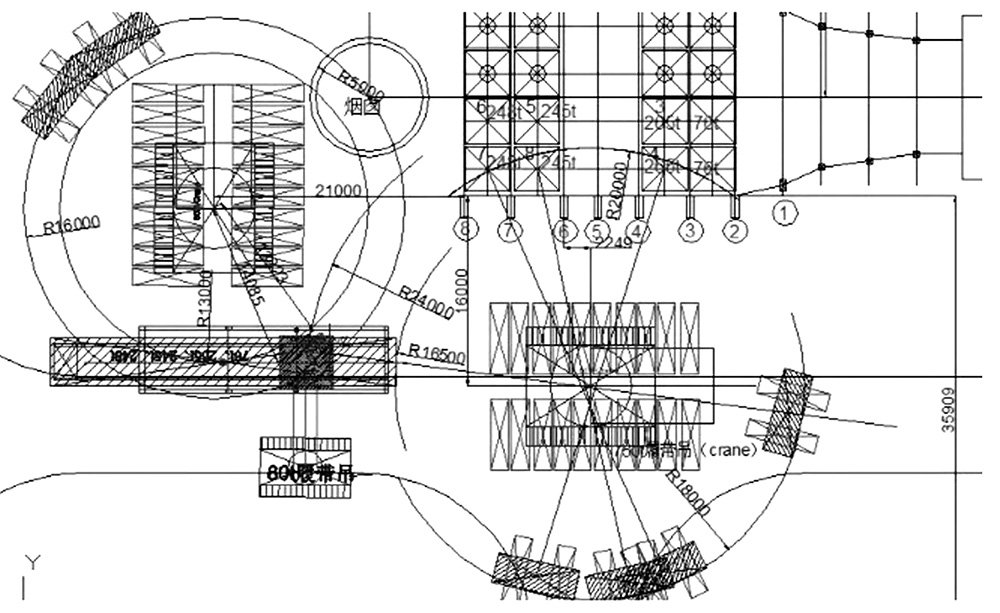
(8) Lifting Height and Space Verification
- The module lifting uses a 750t crawler crane, with a main arm of 79.2m, a super-lift radius of 18m, a steel wire rope folded to 9m, a steel frame height of 30.72m, and an equipment height of 30m. Calculated, it is 0.5m higher than the frame. The verification calculation within a 18.50m radius shows that the distance from the center of the hook to the edge of the arm is 19.01m. After subtracting half the width of the hook, 0.915m, the net clearance is 19.01-0.915=0.996m. It meets the lifting safety requirements.
V. Process Improvement Research
(1) Mechanical Improvement
- If conditions permit, the 750t main crane can be replaced with a larger model; [3] a 400t crawler crane with a super-lift can replace the 500t crawler crane.
(2) Construction Logic Improvement
- Complete the surrounding foundation and other underground facilities in advance, then backfill; the lifting of the two waste heat boiler modules is carried out alternately.
(3) Plan Improvement
- If the manufacturer agrees, the single machine turning and lifting plan can be optimized.
VI. Conclusion
- After researching the lifting process of large modules, its feasibility is demonstrated. Summarizing the on-site implementation experience and further improving the process can provide more references and guidance for similar units in the future.
References:
[1] GB26859-2020. Electric Power Safety Regulations [S].
[2] Italian NE Company. SIR-C1-11-HA_-MGP-NE_-03006NE Waste Heat Boiler Technical Book [M]. Version 02, 2021.
[3] Xu Honglin, Gu Hongkai. A Brief Discussion on the Lifting Process of F-Class Gas Turbine Waste Heat Boiler Modules [J]. Electric Power Equipment Management, 2020 (12): 138-139.